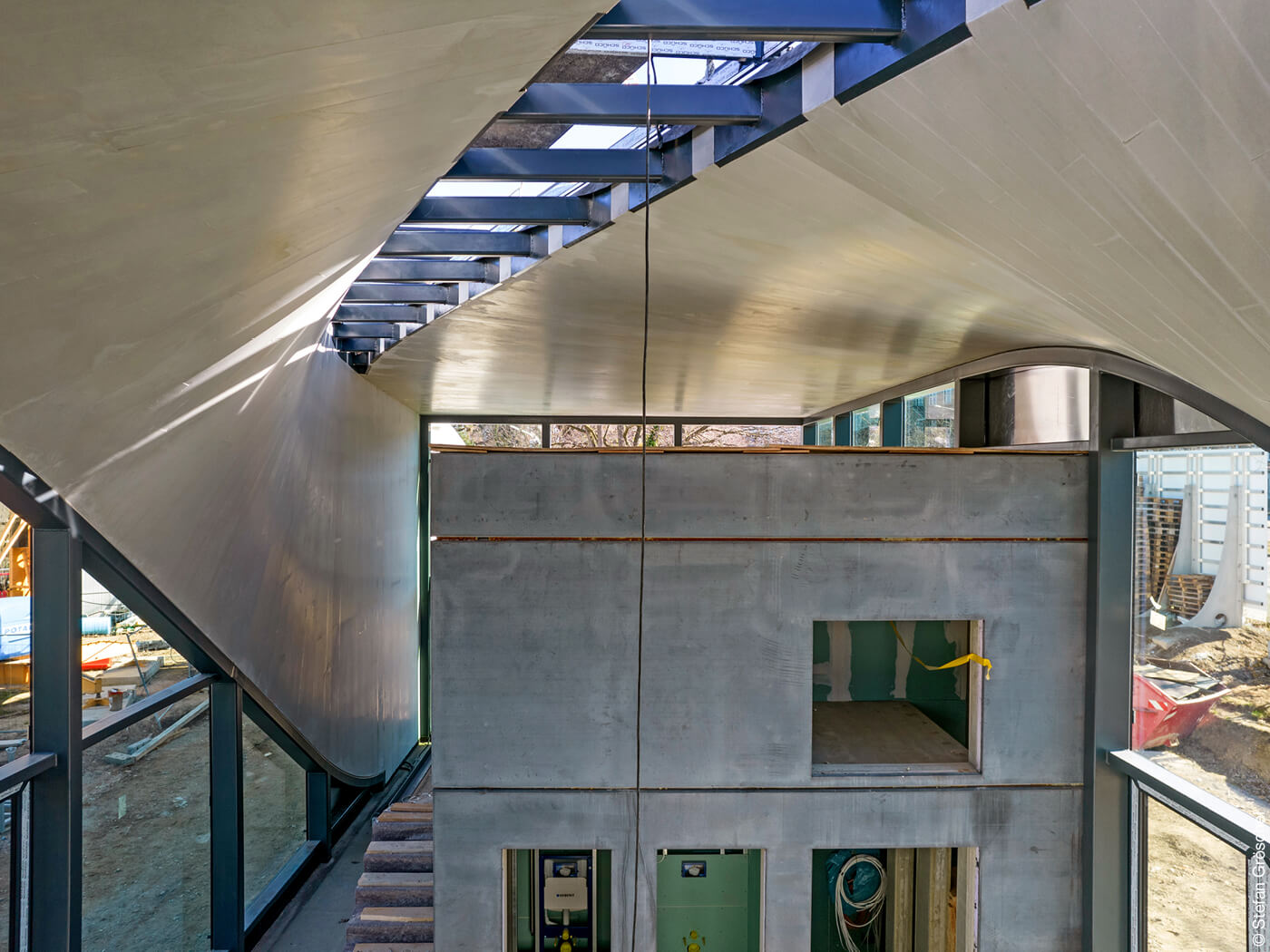
Dieser Beitrag ist unter dem Titel „Let’s do the twist“ im Deutschen Architektenblatt 05.2022 erschienen.
Anfang Februar fand auf der Baustelle an der Ecke Zellescher Weg und Einsteinstraße am Campus der TU Dresden das Richtfest für ein Bauwerk statt, das eine neue Generation der Betonbauweise ankündigt. Gefeiert wurde der im Rohbau fertiggestellte „Cube“ – ein Gebäude, bei dem zum ersten Mal Carbonbewehrung für alle tragenden Betonbauteile eingesetzt wurde. Bauherr ist das Institut für Massivbau an der TU Dresden unter Leitung von Professor Manfred Curbach, der auch Vorstandsvorsitzender des Verbands C³ – Carbon Concrete Composite ist. Das vom BMBF geförderte C³-Konsortium erforscht und entwickelt das Bauen mit dem Verbundwerkstoff Carbonbeton.
Eigenschaften von Carbonbeton
Carbon ist etwa viermal leichter und fünf- bis sechsmal tragfähiger als Stahl und es korrodiert nicht, was die erforderliche Betondeckung auf wenige Millimeter reduziert. Zusammen ermöglichen diese Eigenschaften sehr schlanke Bauteile, die zudem frei formbar sind. Dieses gestalterische Potenzial auszuloten und die massentaugliche Anwendung der Bauweise nachzuweisen, bildeten die Grundlage des Cubes, dessen Design vom Architekturbüro Henn stammt.
Der Cube setzt sich aus der quaderförmigen „Box“ und den „Twist“-Schalen zusammen, die Wand- und Dachkonstruktion vereinen. In Bezug auf die Ausführung erklärt Oberbauleiter Matthias Tietze: „Die einzelnen Bauteile sollten mit üblichen Herstellungsverfahren für Betonkonstruktionen produziert werden. Demnach wurden für die Box Fertig- und Halbfertigteile eingesetzt, die Twist-Schalen entstanden im Spritzverfahren in Ortbetonbauweise.“ Im Fokus der Forschung stand außerdem, den Bauprozess vollständig abzubilden: von der Planung, Zulassung, Kalkulation, Vergabe, Errichtung und Bauüberwachung bis hin zum Betrieb.

Die Box: schlanke Fertigteile aus Carbonbeton
Die geradlinigen Bauteile der Box in Form klassischer Wand- und Deckenkonstruktionen sind im Vergleich zu den geschwungenen Twist-Schalen für die breite Anwendung in der Praxis prädestiniert. Schließlich decken sie ein weitaus größeres Einsatzspektrum ab. Produziert wurden die Box-Bauteile vom Betonwerk Oschatz, die Montage erfolgte durch Bendl HTS. Beide Unternehmen sind seit Langem in das C3-Projekt involviert und hatten im Vorfeld viel Entwicklungsarbeit geleistet.
Die Vorfertigung der Bauteile in einem Betonwerk folgte dem Ziel des Forschungsvorhabens, die gewohnten Abläufe im Bauwesen möglichst wenig zu verändern – hier dargestellt am Beispiel der Wände. Sie wurden als Halbfertigteile auf einer automatisierten Umlaufanlage hergestellt, die üblicherweise der Produktion von Stahlbeton-Halbfertigteilen dient. Die Wand-Halbfertigteile bestehen aus einer Außen- und einer Innenschale aus jeweils vier Zentimeter dickem Carbonbeton mit zwischenliegender Dämmung. Verbunden und auf Abstand gehalten werden die Schichten mit einer Stabbewehrung aus einem Glasfaserverbundwerkstoff.
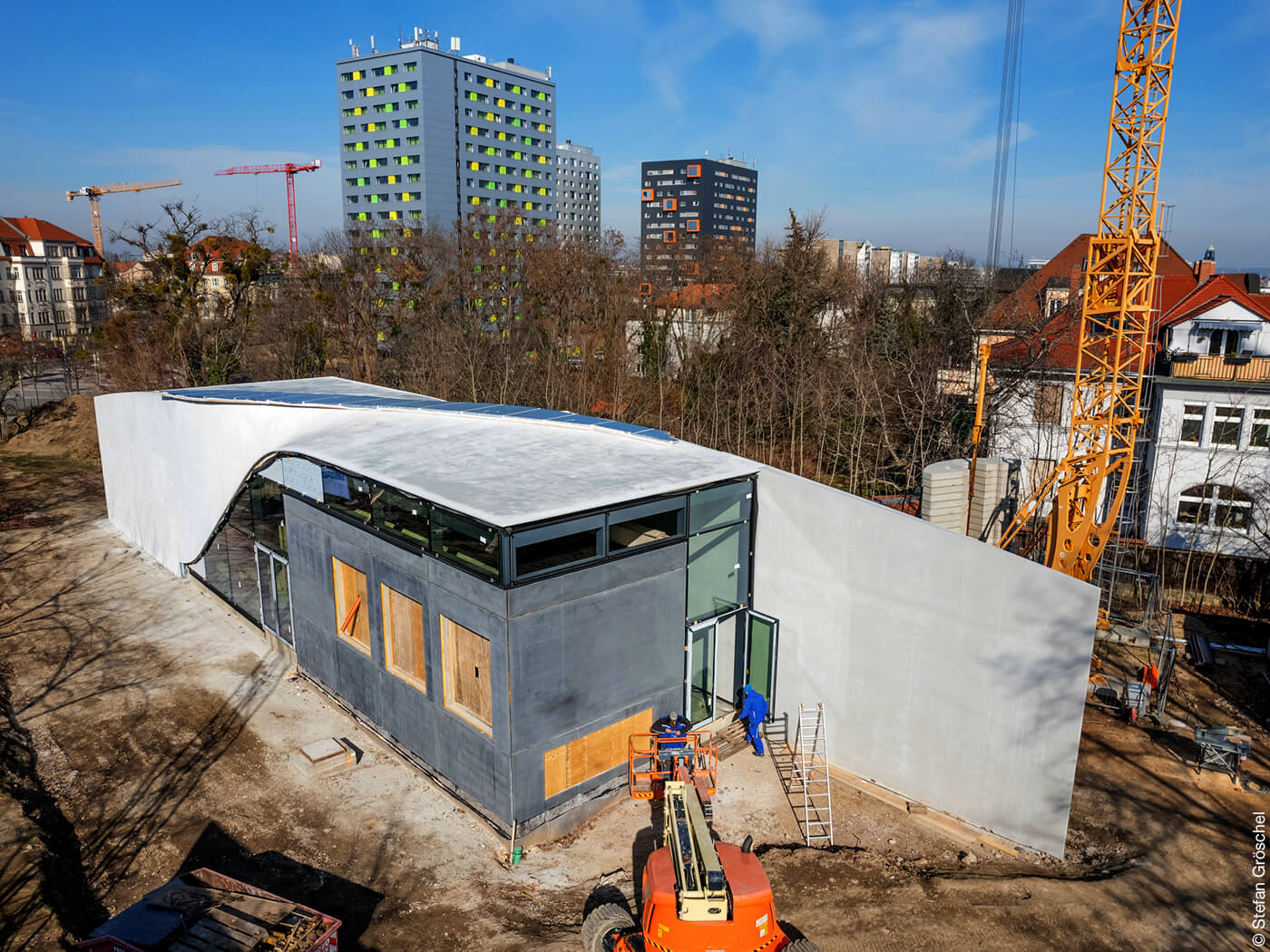
Bei Stahlbeton-Halbfertigteilen sind die Außen- und Innenschale etwa sieben Zentimeter dick und statt der Stabbewehrung werden Gitterträger aus Bewehrungsstahl maschinell eingebracht. „Dagegen musste die Stabbewehrung manuell eingelegt werden, was eine Herausforderung war. Aufgrund der schlankeren Wandscheiben mussten zudem das Handling der Elemente im Werk und der Transport zur Baustelle angepasst werden“, beschreibt Matthias Tietze zwei von zahlreichen weiteren zu lösenden Aufgaben. Aktuell wird unter anderem das Einlegen der Stabbewehrung im Betonwerk automatisiert. Auf der Baustelle hat Bendl HTS die Halbfertigteile dann mit Ortbeton vergossen. Hier waren lediglich ein paar kleinere Einstellungen am Mischer und am Betonausbringkübel nötig.
Der Twist: gekrümmte Schalen aus Carbonbeton
Die Twist-Schalen wurden von der Hentschke Bau GmbH in Spritzbeton auf einer Schalung vor Ort hergestellt. Sie bestehen aus zwei etwa drei Zentimeter dicken Betonschichten, in die jeweils Bewehrungsmatten aus Carbon eingelegt wurden. Zwischen den Schichten befinden sich Hohlkörper. Auf diese Tragschale wurde eine Abdichtung aufgebracht, darauf die Dämmung verlegt und abschließend eine vier Zentimeter dicke Wetterschale aus Carbonbeton aufgebracht.
Die Ausführung der Twist-Schalen war deutlich aufwendiger als die der Box-Bauteile. „Mit einer Arge aus Bendl HTS und Hentschke Bau wurde explizit eine Generalunternehmer beauftragt, um nicht jedes Gewerk einzeln ausschreiben zu müssen“, erklärt die für die Generalplanung zuständige Architektin der AIB Architekten Ingenieure Bautzen GmbH Marén Kupke. Schließlich sind an den Carbonbetonbauteilen auch viele andere Bauteile, wie Installationen jeglicher Art, befestigt oder mit ihnen verbunden.
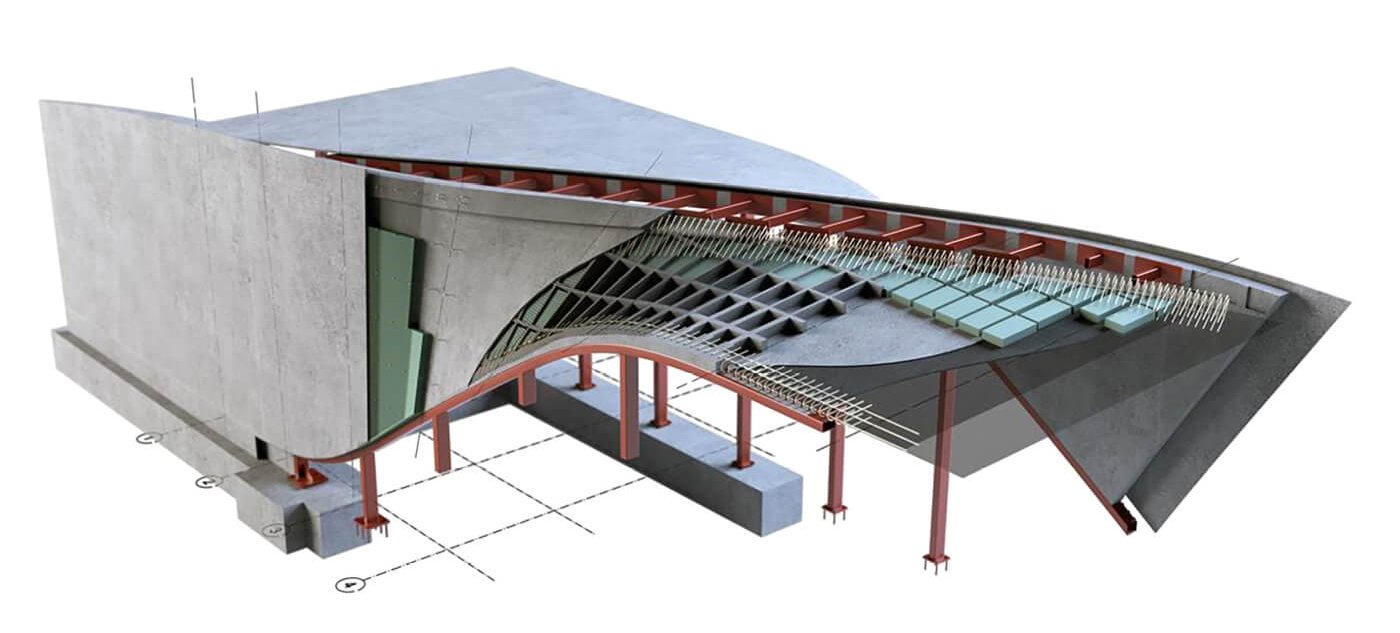
Planung und Ausschreibung
Ob bei den Twist-Schalen oder der Box: die Einmaligkeit der Bauaufgabe erforderte die intensive Zusammenarbeit aller Beteiligten. Das spiegelt sich auch bei der Ausschreibung der Bauleistungen wider, die von Michael Frenzel vom Institut für Massivbau der TU Dresden in Zusammenarbeit mit Marén Kupke, AIB Architekten Ingenieure Bautzen, erstellt wurde. Das Problem war: „Die noch nicht zugelassenen Bauteile machten eine rechtssichere Ausschreibung unmöglich. Man konnte also nicht auf Standardleistungstexte, anerkannte Regeln der Technik etc., zurückgreifen. Deshalb haben wir für die Vergabe der Bauleistungen ein Verhandlungsverfahren mit einer funktionalen Leistungsbeschreibung gewählt, in der jedes Bauteil durch Anforderungen und Qualitätsziele beschrieben wird.“
Allein die Formulierung dieser Zielstellungen war eine Herausforderung und nahm viel Zeit in Anspruch, erinnert sich die Architektin. Auch Kosten-, Zeit- und Personalaufwand konnten aufgrund fehlender Vergleichsprojekte und Erfahrungswerte nur geschätzt werden und mussten im Planungs- und Bauablauf mehrmals angepasst werden. Aber im Endeffekt hat sich die Arbeit gelohnt, denn für die Überführung der Bauweise in die Praxis können Interessenten nun auf die Konstruktionsbeschreibungen und Detailzeichnungen des Forschungsprojekts zurückgreifen und sich zudem von Marén Kupke beraten lassen.
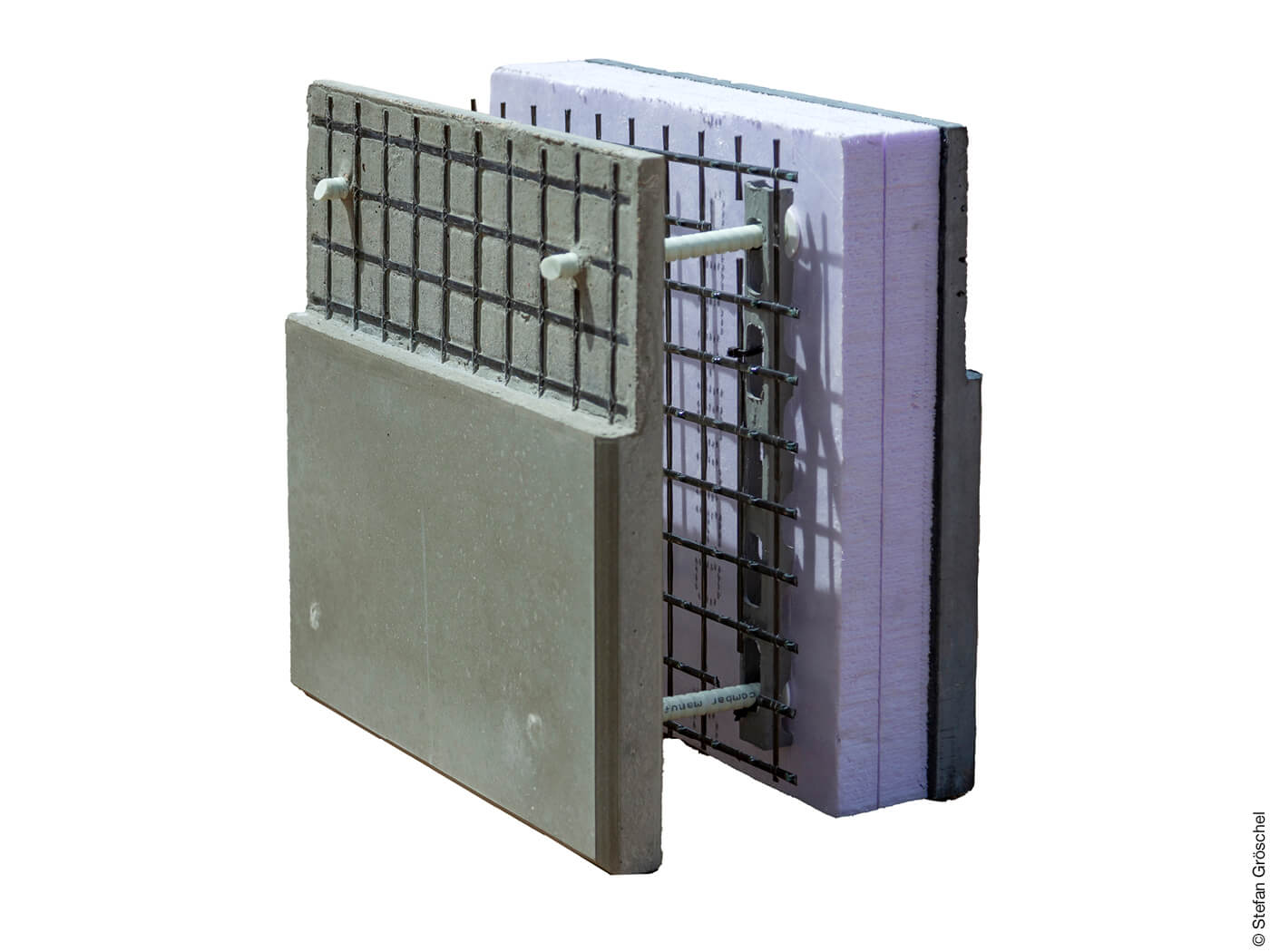
Zulassungen im Einzelfall
Zurückgreifen können potenzielle Bauherren auch auf die zahlreichen Zustimmungen im Einzelfall, die während der Bauausführung des Cubes für alle Carbonbetonbauteile erwirkt wurden. Die Komponenten der Bauteile wurden jeweils einzeln und dann als Bauteil geprüft. Sollen die Bauteile in weiteren Projekten eingesetzt werden, ist zwar nach wie vor eine Zustimmung im Einzelfall erforderlich, „auf Basis unser Grundlagenversuche, deren Ergebnisse wir zur Verfügung stellen, vereinfacht sich aber das Antragsverfahren bei der Baubehörde deutlich“, erläutert Matthias Tietze.
Im Zuge der bauaufsichtlichen Zulassungsverfahren wurden auch ein Recyclingbeton und ein selbstverdichtender Beton geprüft, die für den Einsatz im Carbonbetonbauteil entwickelt wurden. Da Recyclingbeton verdichtet werden muss, entschied man sich aufgrund des einfacheren Betonierens beim Cube für die selbstverdichtende Variante.
Noch teuer aber dafür Flächengewinn
Von den technischen Vorteilen des Carbonbetons sind die meisten Baufachleute sicher schnell überzeugt. Entscheidend ist: Wie wirtschaftlich ist die Bauweise? Matthias Tietze sagt: „Die Carbonbetonwände sind sehr schlank, woraus sich ein erheblicher Flächengewinn ergibt. Die Außenwände der Box sind bei einem U-Wert von 0,19 W/(m2K) 27 Zentimeter dick, in Stahlbeton wäre aufgrund der dickeren Betonschalen und der konventionellen Dämmung eine Dicke von 44 Zentimetern erforderlich.“ Der Flächengewinn sei ein Effekt mit Sofortwirkung für den Investor, so Tietze weiter. Das bestätigten auch Projektentwickler, die nach der Präsentation des Cubes vor Ort am Einsatz des Wandsystems interessiert sind – trotz des im Vergleich zu Stahlbetonwänden doppelt so hohen Preises.
Die Kosten würden allerdings bald sinken, denn die Differenz resultiert zurzeit noch aus dem Mehraufwand der noch nicht gänzlich voll automatisierten Herstellung. Der Prozess soll bis nächstes Jahr abgeschlossen sein, dann „dürften die wie bei Stahlbeton üblichen Herstellungskosten und -zeiten erreicht sein“, ist sich Matthias Tietze sicher.
Carbon und Stahl im Preisvergleich
In die Kalkulation spielt natürlich auch der Preis für die Carbonbewehrung mit hinein. Stahl ist im Vergleich zu Carbon deutlich günstiger, doch die Leistungsfähigkeit von Stahl ist geringer. Carbon kann fünf- bis sechsmal mehr Zugkräfte aufnehmen, sodass weniger Bewehrung benötigt wird. Zusammen mit der niedrigeren Dichte von Carbon ergibt sich ein Preisfaktor für Carbon vom 10- bis 15-Fachen, der Leistungsfaktor liegt aber bei etwa dem 20-Fachen. Damit ist Carbon als Bewehrungsmaterial schon jetzt leistungsfähiger als Betonstahl.
Bei den Twist-Schalen ist die Rechnung nicht so einfach. Hier schlagen die individuelle Schalung sowie die aufwendige Herstellung für die gekrümmten Elemente mit hohen Kosten zu Buche. Genau wird man es wissen, sobald das Gebäude fertiggestellt ist. Denn zu den Aufgaben von Marén Kupke gehören im Rahmen des C3-Projektes auch eine detaillierte Kostenzusammenstellung für Box und Twist sowie eine Nachhaltigkeitsbetrachtung.
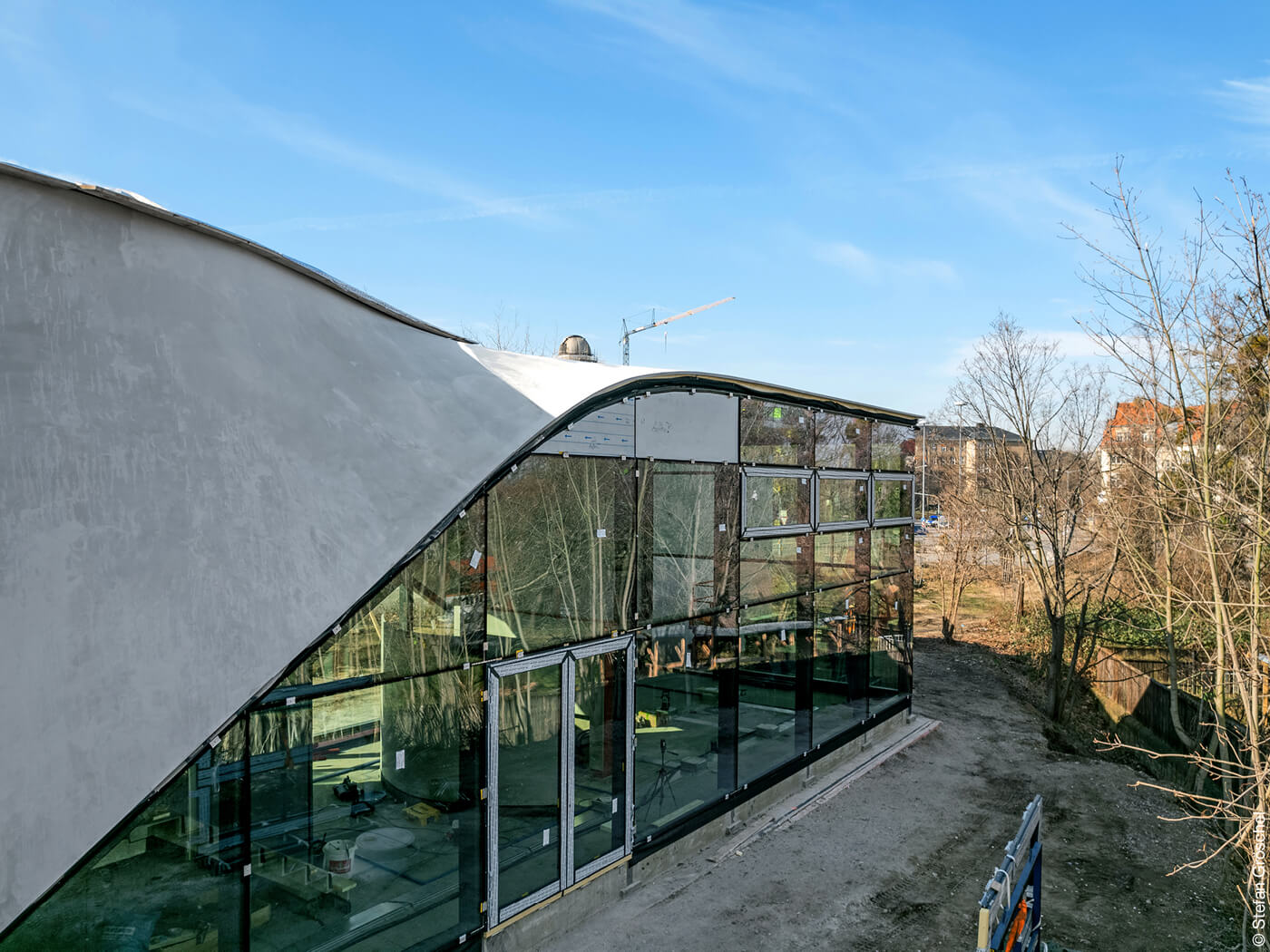
Markteinführung angelaufen
Die Eröffnung des Cubes ist für September 2022 geplant. Dann ist auch das C3-Forschungsvorhaben beendet. Wesentliche Schritte zur Etablierung der Carbonbetonbeweise in der Praxis sind jedoch schon jetzt eingeleitet. So fusionierten der C³ - Carbon Concrete Composite e. V. und der Tudalit e. V. zum größten Industrie- und Forschungsverband für Carbonbeton. Im neuen C³-Industrieverband werden weiterführende Projekte gestartet, die unter anderem Themen wie die Standardisierung der Bauweise (ISC-RUBIN), bauaufsichtliche Zulassungen oder das Schließen von Stoffkreisläufen (WIR!-recyceln-Fasern) vorantreiben.
Maßgeblich für den Einsatz von Carbonbetonwänden und -decken ist ihre Bereitstellung durch möglichst viele Betonwerke. Aktuell ist das Betonwerk Oschatz für ihre Herstellung qualifiziert. „Zurzeit sind wir mit einem mobilen Einsatzteam bundesweit unterwegs und stellen die Produktionstechnologie anderen Betonwerken vor“, sagt Matthias Tietze.
War dieser Artikel hilfreich?
Weitere Artikel zu:
Hört sich gut an, gerade zur Möglichkeit dünner Schalen. Aber insbesondere der Korrosionsfrage. Einzige Frage, die für mich noch im Raum steht, ist, wie sich der Beton im Spannungsverhalten der unterschiedlichen Temperaturbereiche der Jahreszeiten verhält und wie das Schwundrissverhalten ist.